Having searched far and wide for my unicorn handlebar, it occurred to me the only way I’ll get exactly what I want is to make it. I have a bit of carbon and laminating experience so I feel comfortable enough to consider having a go, but obviously if something fails I could break my face or worst still my bike.
So, does anyone have any experience making custom carbon drop handlebars? Specifically I need advice on material choices and lay-up - I’m thinking mostly unidirectional for optimum strength, but how to work out how many plies and what orientation? I’m not too fussed about weight, but some comfort/compliance would be good. Would prepreg yield a significantly better final product, versus wet lay-up? I don’t have the tools or knowledge to do prepreg so if wet lay-up won’t work then I’ll most likely can the whole idea!
For reference, I’m after making a narrow and flared all-road/gravel bar, with grooves for brake hoses that extend underneath the stem clamp (like how Cervelo do it on their road and gravel bars). Ideally I want the general shape of the Lambda Cross-Wing but with a round top and a bit of backsweep/upsweep (like the Coefficient AR but not quite as much). My riding weight is around 100kg, I do mostly rough tarmac and light/medium gravel.
Using a female mould with internal vac bag should be simple enough. I suppose taking a mould from an existing bar and modifying it might be simpler than learning CAD, designing and 3D printing something, but perhaps not? I’ve looked up the ISO testing for handlebars, without access to a testing rig I might be limited to a less-stringent cyclic test and a max load/failure test. I reckon I’d start by making a straight tube or simpler handlebar shape first, test it and ride it, then iterate and improve as needed before finalising the shaping. Or maybe that makes no sense and I should just make the first prototype the shape I want and then I can test that too!
4 Likes
Even though I haven’t done any carbon work myself, I have enough of an engineering background to know that the type of questions you’re asking here doesn’t give me confidence that you’re capable of making such a safety critical component yourself.
2 Likes
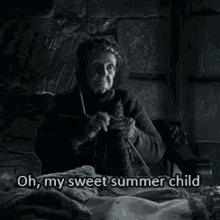
A female mould and internal vacuum bag will be challenging as the internal diameter of a handlebar is small, fiddly, and full of peculiar curves. Pre-preg will make it a lot easier but will require more expensive tooling and an oven large enough for it.
Honestly. If you’re looking to make a one off and you’re solely interested in the shape and features of it, then creating some sort of internal core to layup over will give you the best chance of making something that cold be safe to ride.
Sounds like a fun project so give it a go. But be wary of assuming the simplicity of certain processes.
I haven’t done this but had considered it (and in the end went the CNC bending / metal route). But here is the strategy I came up with:
The basic idea is to 3d print the shape of the handlebars and then lay the carbon fiber around that shape. You won’t be able to print the whole form as one piece so you would need to print separate pieces and design a “sashimono” style connection into the ends of the individual pieces. But those connections don’t have to be absolutely perfect because you can additionally glue over them. The easiest way would be to print that form from water soluble PVA, then lay just one layer of carbon (to limit the heat the PVA is exposed to), wait until it has cured, then lay the rest of the layers. At the end you can wash out the PVA with water.
The challenge with this approach is the heat generated through the exothermic reaction of the epoxy (i.e. the reaction of resin with the hardener) could deform the PVA because PVA isn’t very heat resistant.
How much heat will be produced during the curing of one layer of “epoxy wet lay carbon fiber”? Based on https://m.youtube.com/watch?v=3uzRaSJFWo4 the maximum temperature was 103° F = 39.4° C. And that was a higher volume per area of epoxy than the volume per area for one layer (and probably also for several layers) of carbon/epoxy. So max temp should be below 39.4°C.
Above what temperature does PVA loose it’s rigidity? My own conclusion is that there should not be any significant effect on the shape of the 3d printed part under 40°C. This conclusion is based on comparing a) the temperatures at which the parts loose their form in https://m.youtube.com/watch?v=QdAKd_YbsjI&pp=ygUPUHZhIHRlbXBlcmF0dXJl (min 17.30) with b) the ISO 75 values of PVA, PETG at Filaments – ROSA3D.
What helps additionally to limit the heat during curing is to let it cure in a ~22°C environment (definitely not above 25°C). Acc to https://m.youtube.com/watch?v=mafN8GFZfas&pp=ygUXRXBveHkgaGVhdCB0ZW1wZXJhdHVyZSA%3D the ideal temperature is 22° to 27°
Whether it works or not depends on the actual heat resistance of the PVA and the heat generated by the epoxy but for a one off project it’s the easiest method I think. I would definitely make some tests (does the PVA deform etc) before committing to it.
Another option would be CNC bending a metal tube into the shape you want. Bending radius down to 1.5 times the diameter are possible with the right machines.
I should also say that I am not a seasoned carbon professional. Just a hobbist with ideas. Keep that in mind with a safety critical part like this.
1 Like
That’s great you’ve got some carbon experience! The hard part of making a carbon bar for your first design project isn’t the physicality of manufacturing the part.
I often get folks asking me if they could build X or make Y. My concise response is, if you have to ask… you probably shouldn’t make it yourself.
The long answer is, spend the 100’s or 1000’s of hours developing the process and figuring out the materials required to acheive your bar build. There’s really no other way than learning from a whole lot of failure before you succeed
Also, a handlebar wouldn’t be great first design project. Start small and non structural.
2 Likes